In the world of plastic manufacturing, precision and innovation go hand in hand. At our CNC machine shop, we recently embarked on a fascinating journey of developing a Rotomoulding mold for a new plastic product. This endeavor was not only a testament to our technical capabilities but also a showcase of our commitment to pushing the boundaries of what’s possible on our machines. In this blog post, we’ll take you through the step-by-step process of how we conceptualized, designed, and manufactured the rotomoulding form for a polyethylene tub, highlighting the expertise and dedication that went into bringing it to life.
Understanding the Requirements:
Every successful project begins with a clear understanding of the requirements. In the case of the rotomoulding form, we worked closely with our company division that sells and services tyre-shop equipment. We discussed factors such as product dimensions, material properties, and production volume to ensure that our solution would meet their exact specifications.
Concept and Design of the tub:
Armed with a thorough understanding of the requirements, our designer set out to conceptualize the shape and design of final product. This involved brainstorming ideas, sketching preliminary designs, and leveraging computer-aided design (CAD) software to create detailed 3D models. Throughout this process, we focused on optimizing the product for efficiency, durability, and ease of use, keeping in mind the unique challenges posed by the rotomoulding process. After settling up on final shape of the product we performed non-linear shell FEM analysis of the product to verify structural soundness of the design.
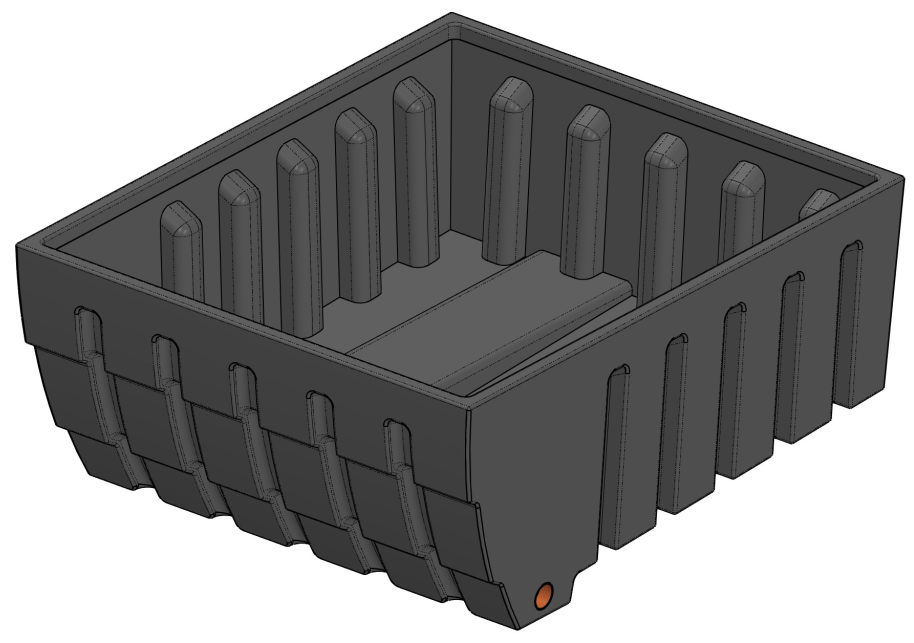
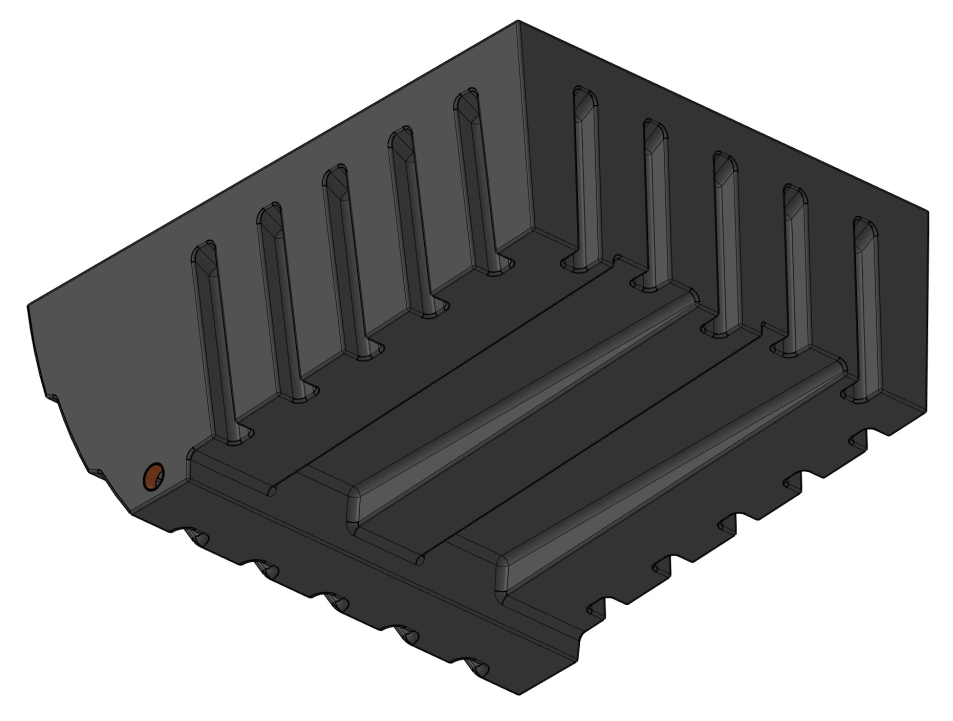
Mold Design:
With the design of the plastic product finalized, we moved on to the design phase of the mold itself. Mold was designed in Solidworks and split into 8 separate pieces to make the manufacturing feasible on 3 axis milling machine as well as save on the cost of aluminim. Those 8 separate pieces were later welded together to form the base and lid of the mold. The mold itself also needs to account for stainless steel and on 1/2 inch brass inserts that will be incorporated during every pour and will create interface where the rest of the machine can be bolted on.
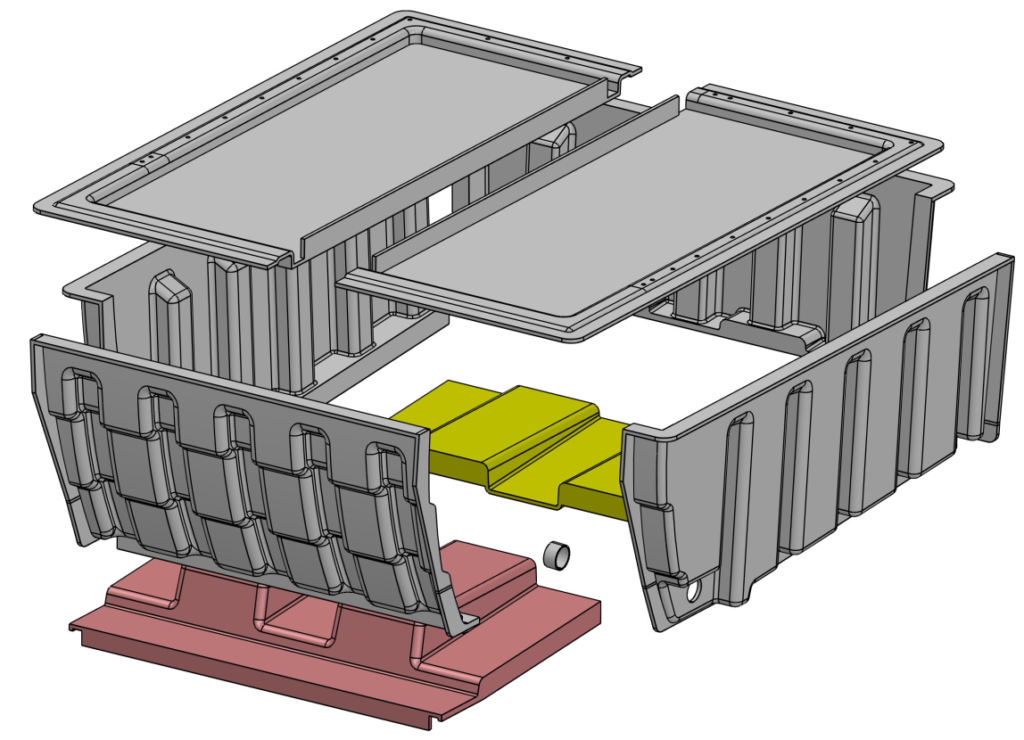
Mold Manufacturing:
With the design finalized, we moved on to the manufacturing phase. Using our state-of-the-art CNC machining capabilities, we fabricated 8 separate pieces of the mold from solid cast aluminium blocks that were later on welded together. Each component was carefully machined, cleaned, and inspected to ensure a perfect fit and finish of all pieces of the puzzle. Throughout the manufacturing process, we maintained open lines of communication with our partner CZ-PLAST s.r.o. that was chosen to do the molding process itself, providing regular updates and addressing any concerns that arose. After machining of all the pieces the mold was welded together by our skilled welders and special method of stell beads-blasting was utilized that gives the product its final surface texture. Last step of production was the design of frame that attaches to furnaces gimball and thermal insulation of areas we dont want plastic material to adhere to.
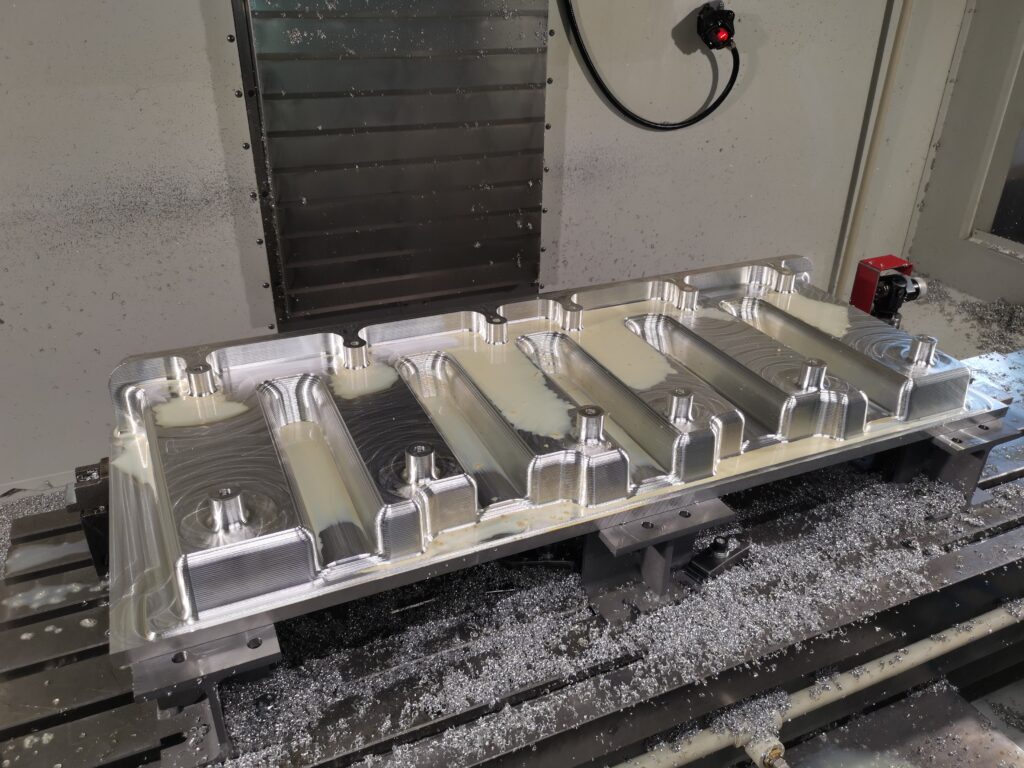
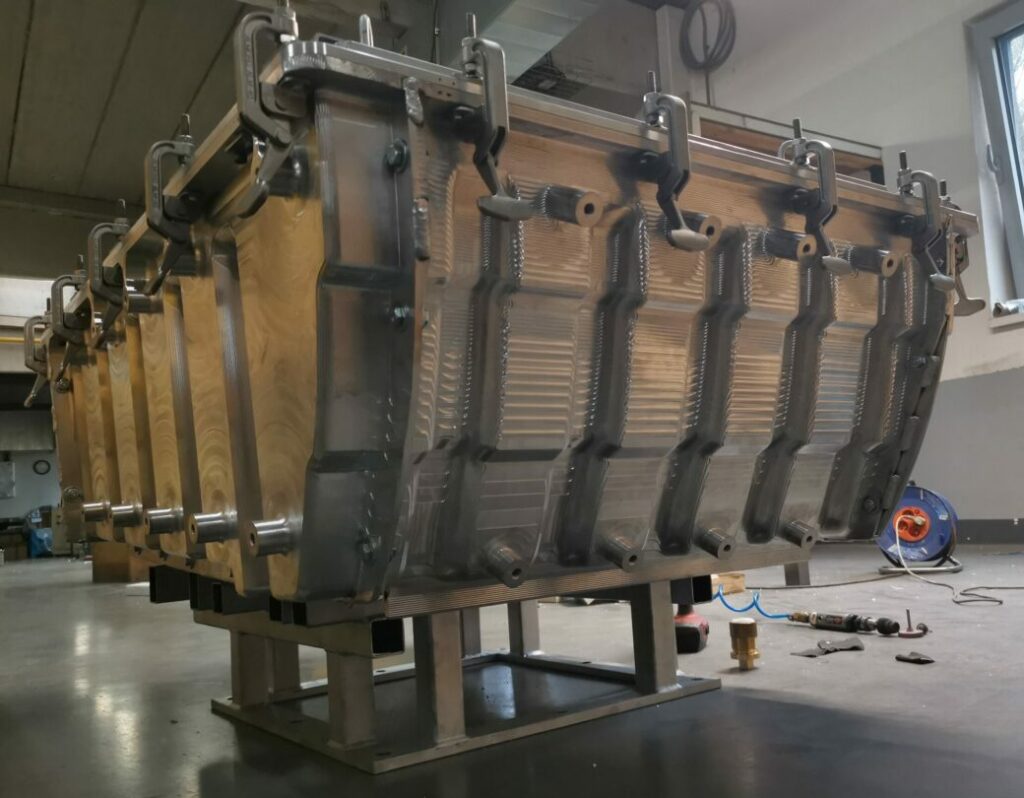
Testing and Validation:
Before delivering the rotomoulding form to CZ-PLAST s.r.o., we ensured that all the desired requirements were met. This included simulated rotomoulding trials, dimensional inspections, and material compatibility tests. By subjecting the form to real-world conditions, we were able to identify and rectify any potential issues, ensuring that it would meet our client’s expectations and deliver optimal results.
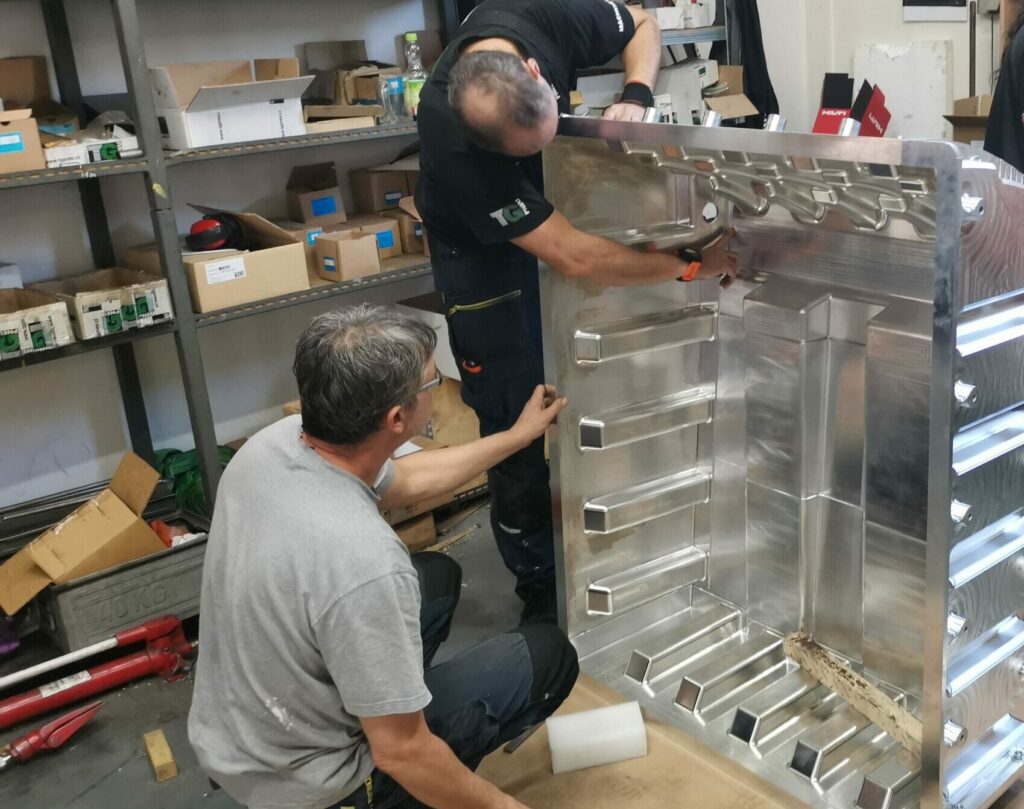
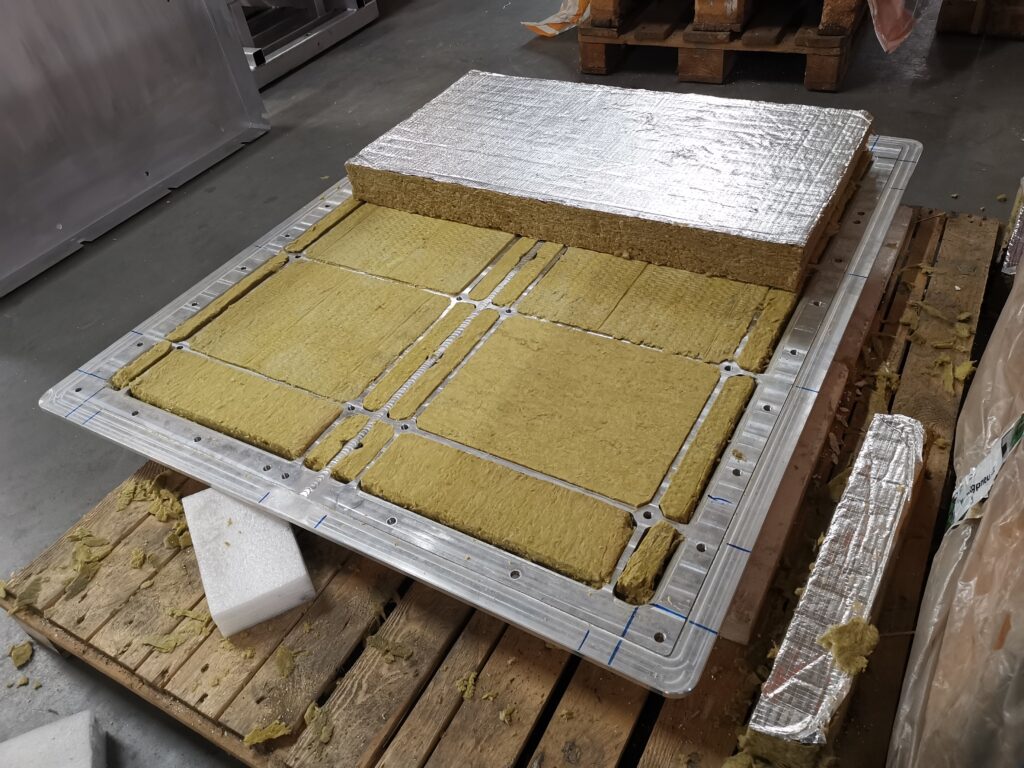
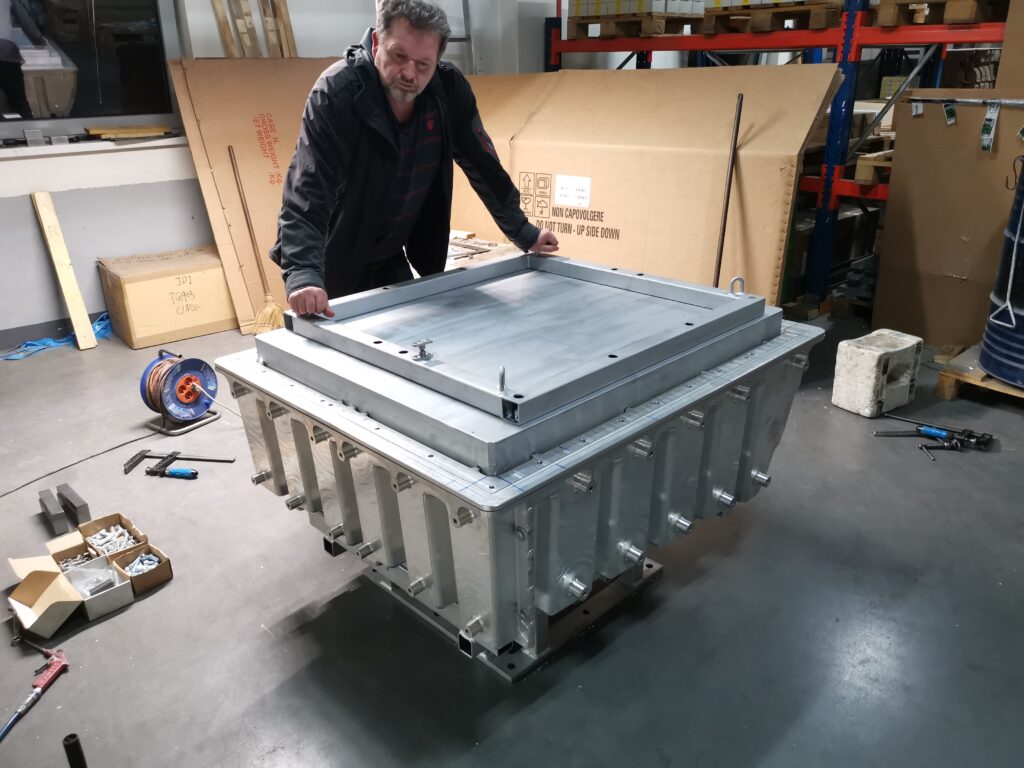
Conclusion:
Precision and dedication to end result is at the heart of everything we do at our CNC machine shop, and the development of the rotomoulding form is a shining example of our commitment to excellence. From conceptualization to production, every step of the journey was guided by a relentless pursuit of quality and precision. As we continue to push the boundaries of what’s possible, we look forward to embarking on new challenges and delivering innovative solutions that exceed our clients‘ expectations.
Do you need mold for your product
We can cover the whole journey from concept to molding trials…
Final product can be seen on video below :
Leave a Reply